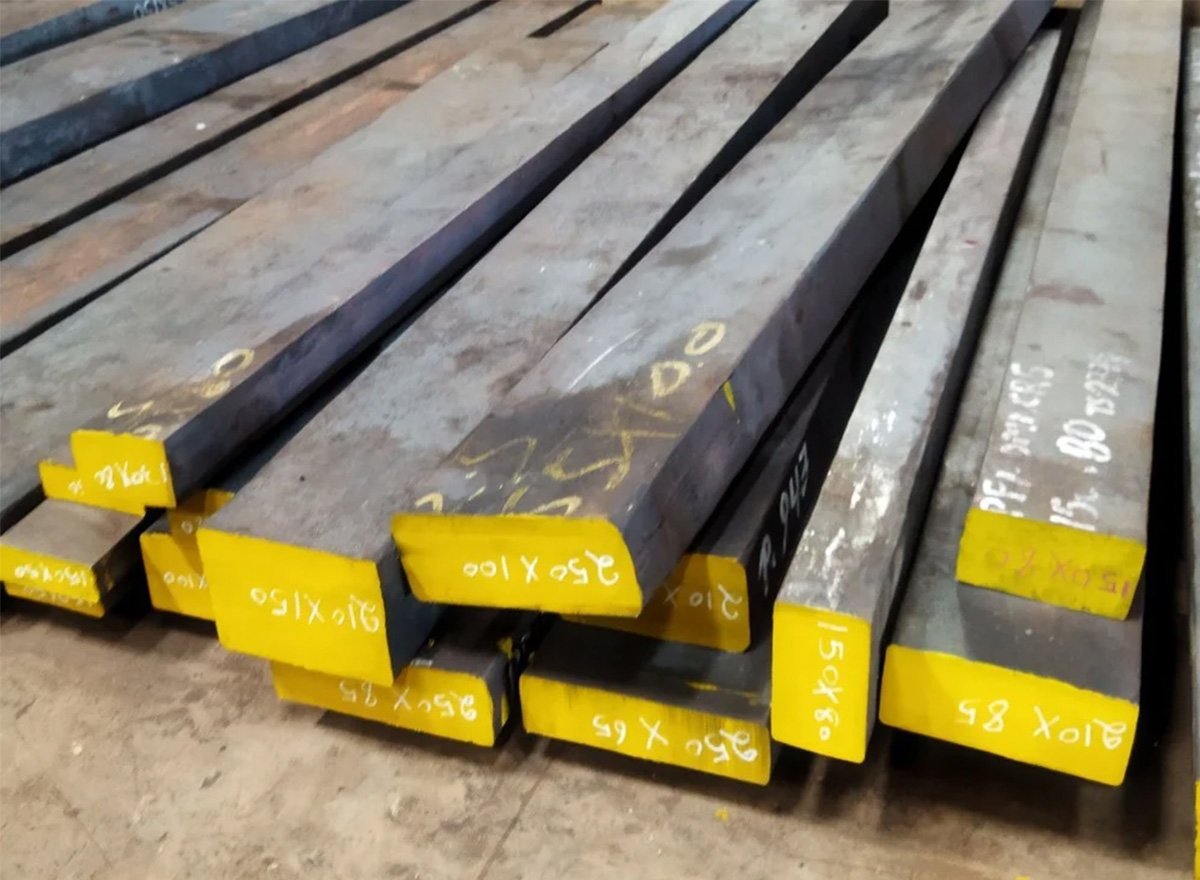
Tool steels, known for their exceptional strength, wear resistance, and heat tolerance, are a class of high- carbon and alloy steels extensively utilized in the manufacturing of cutters, reamers, bits, and other tools for machining metals, plastics, and wood. These steels typically incorporate elements such as cobalt or nickel to enhance strength and high-temperature performance. Additionally, carbide-forming elements like chromium, vanadium, molybdenum, and tungsten are included in various combinations to improve hardness and wear resistance. Tool steel production primarily takes place in electric arc furnaces, where the material is melted, purified, and adjusted to the desired composition. The molten steel is then poured into ingots, cooled, and annealed to prepare it for subsequent processing. Advanced production techniques, such as powder metallurgy, are also employed for specialized applications, ensuring superior performance and material uniformity.
Key Features of Tool Steels:
- Carbide-Forming Metals: Elements like chromium, molybdenum, tungsten, and vanadium contribute to exceptional hardness and wear resistance.
- Substitutional Solutes: Additives such as nickel and cobalt enhance strength, particularly at elevated temperatures.
- High Carbon Content: Enables the formation of strong carbidesÂ
Hot work die steels are premium-grade materials designed with precise compositional and physical tolerances. These steels are essential for manufacturing dies used in shaping and forming materials into specific components for industrial applications. Their versatility makes them ideal for processes such as hot forging, pressure die casting, extrusion, and the production of tube and glass products. Due to their superior performance and durability, hot work die steels are widely employed in the mass production of tools for shaping and forming metals, plastics, and other materials.
High-speed steel (HSS) is a specialized alloy designed for high-performance cutting tools. Comprising over 40 tool steel alloys, HSS contains 0.7%-1.65% carbon and 10%-25% alloying elements such as tungsten, molybdenum, chromium, vanadium, and cobalt. The inclusion of these elements ensures exceptional hardness, heat resistance, and cutting efficiency.
Applications of High-Speed Steel:
- Manufacturing cutting tools: drills, taps, milling cutters, and tool bits
- Production of gear-cutting tools: such as hobbing cutters and broaches
- Fabrication of power saw blades, planer and jointer blades, router bits, punches, and dies
- Used in lathe tools and turning tools for precision machining
- Application in cold work tooling such as blanking and forming dies
- Production of high-performance cutting blades for industrial and woodworking applications
- Used in metal stamping and forming operations due to its durability and wear resistance
- Manufacturing of surgical instruments requiring high strength and edge retention
Product Category | Product Name |
---|---|
High-Speed Steel (HSS) | M2, M35, M42, T1, T4, T42 |
ASP 23, ASP 30 | |
Hot Die Steel | H11, H13, H21 |
Tool Steel | OHNS, 1% Carbon, S1, S7, A2 |
DIN 2714 | |
Plastic Mould Steel | P20, P20 + Ni |
High Carbon High Chromium (HCHCR) Tool Steel | D2, D3, KNL |
2379 |